Case Study
Achieving Peace of Mind with Spare Gearboxes
Particularly for smaller operations, purchasing spare industrial gearboxes may seem cost-prohibitive or unnecessary. But given the high costs associated with unplanned downtime in mission-critical processes, the return on investment is often worth it. Ted Pratt, account specialist at Philadelphia Gear®, shares how keeping spare gearboxes in inventory can help maintenance teams address equipment challenges before they lead to catastrophic shutdowns.
Q: If a gearbox does go down, what is the average lead time for a repair or replacement?
A. For an expedited repair — the costliest to procure — lead times still range from two to six weeks. Standard repairs often take about 15 to 25 weeks, with new gearboxes currently taking 25 to 35 weeks due to ongoing supply chain challenges and the complexity of customized gearbox design and manufacturing. So again, it’s important to think about the cost of potential downtime. An investment of $200,000 in a backup gearbox for a major process in your operation is far more cost-effective than even just a few days of downtime at $100,000 a day.
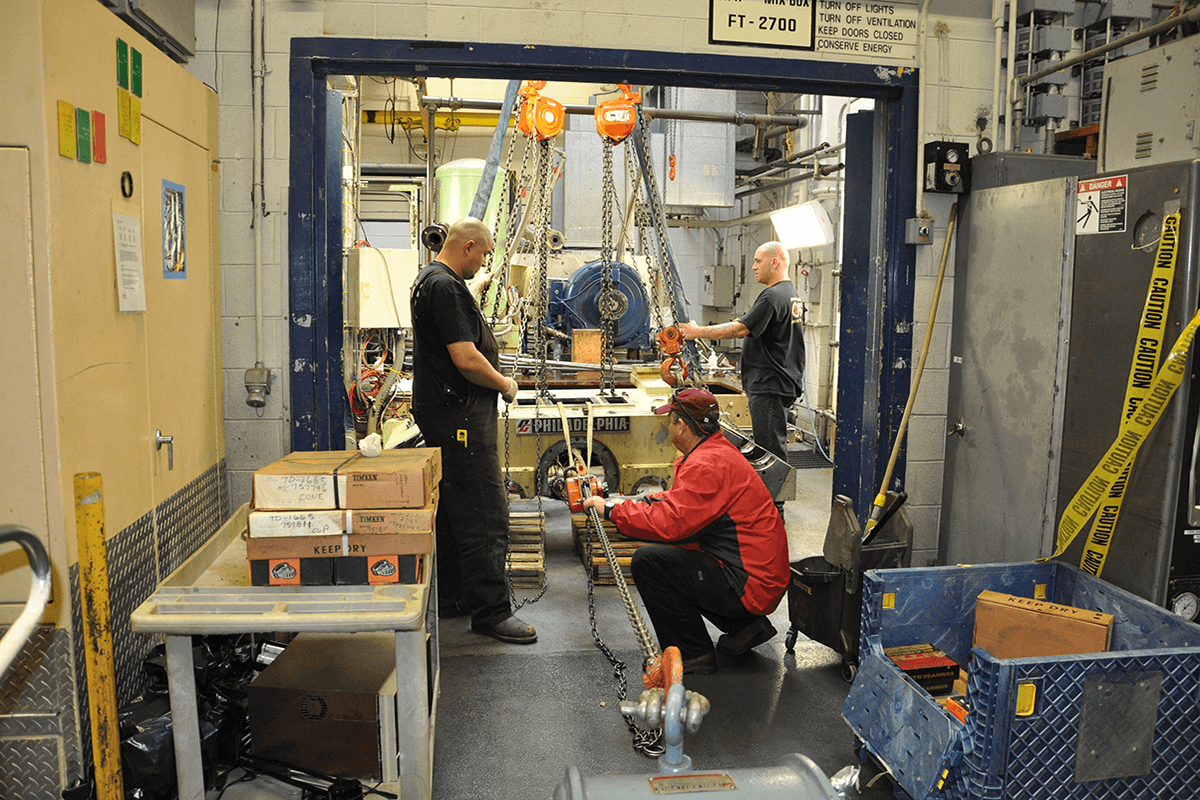
Q. Ted, in your experience, which industries or applications benefit most from keeping spare gearboxes on hand?
A. My honest answer is all of them. However, it does depend on the industry and how much of an investment a company can make. The power generation industry – including coal and gas-fired power plants and hydroelectric operations – is one that especially benefits. Their product is electricity, and you can’t stockpile that in case of an emergency. If a power plant goes down, they must purchase power from the grid to fulfill their contracts, and that’s very costly.
Most oil and gas producers opt for keeping spare gearboxes as well because it’s crucial to maintaining their revenue streams. Many have duplicate production operations in addition to backup gearboxes so that if one line goes down, they always have the capability to keep producing and delivering products.
Power and oil and gas are industries where the cost of failure is high. Knowing what one hour, one day or one week of downtime costs your company is the key to understanding if investing in spare gearboxes is the right move for your business and operations.
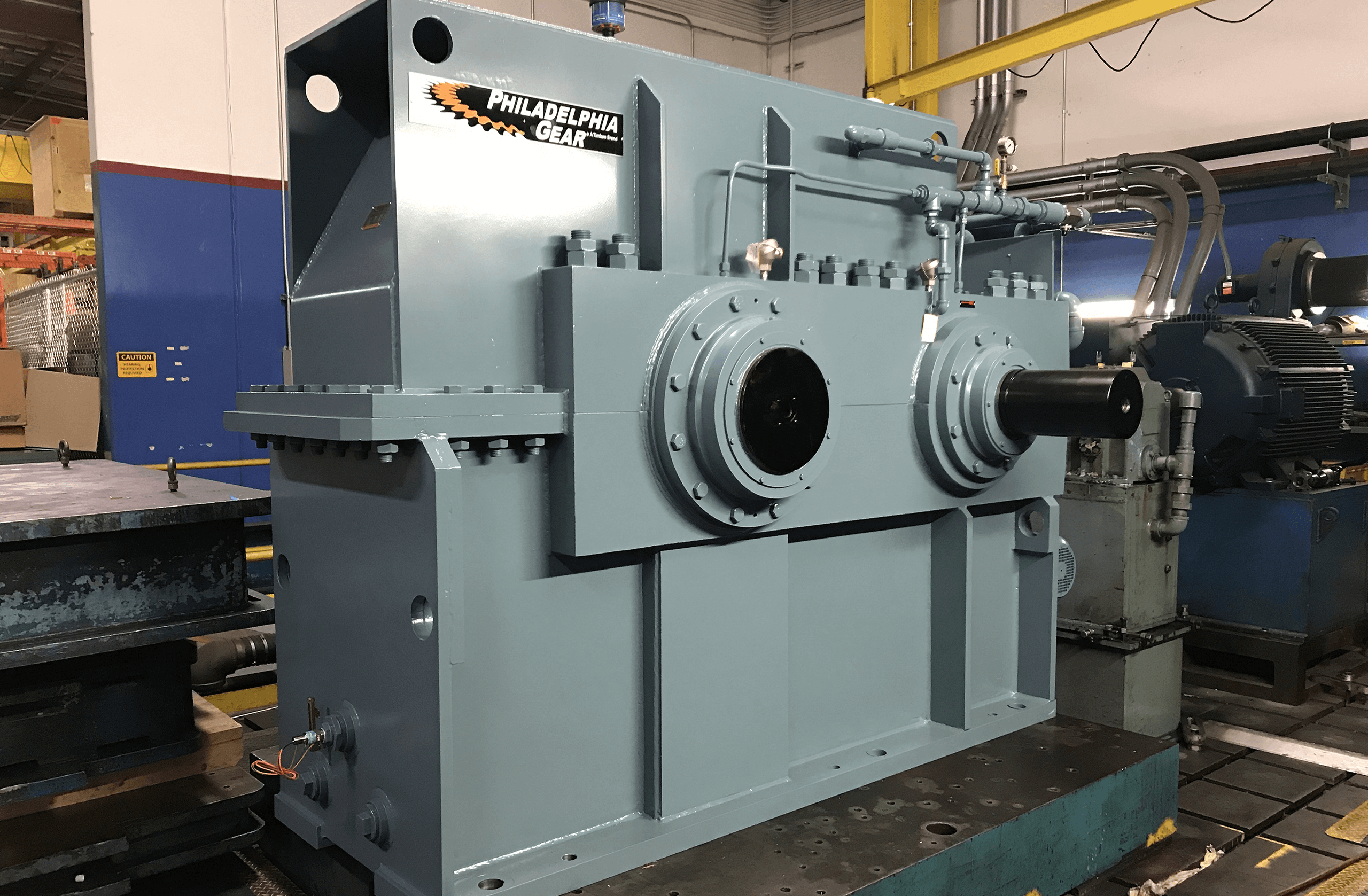
Q: What’s the potential revenue loss when a gearbox fails?
A. It can range from thousands to millions of dollars, but I can give you an example. Recently, an aging gearbox in one of our cement customers’ operations failed during the height of construction season. It resulted in more than $1 million in revenue loss and created a ripple effect. Their cement distributors had to furlough drivers due to the supply shortage, and construction sites had to find other sources for cement or delay their projects. The experience motivated the customers to add a second production circuit at their site and add a spare gearbox to their inventory.
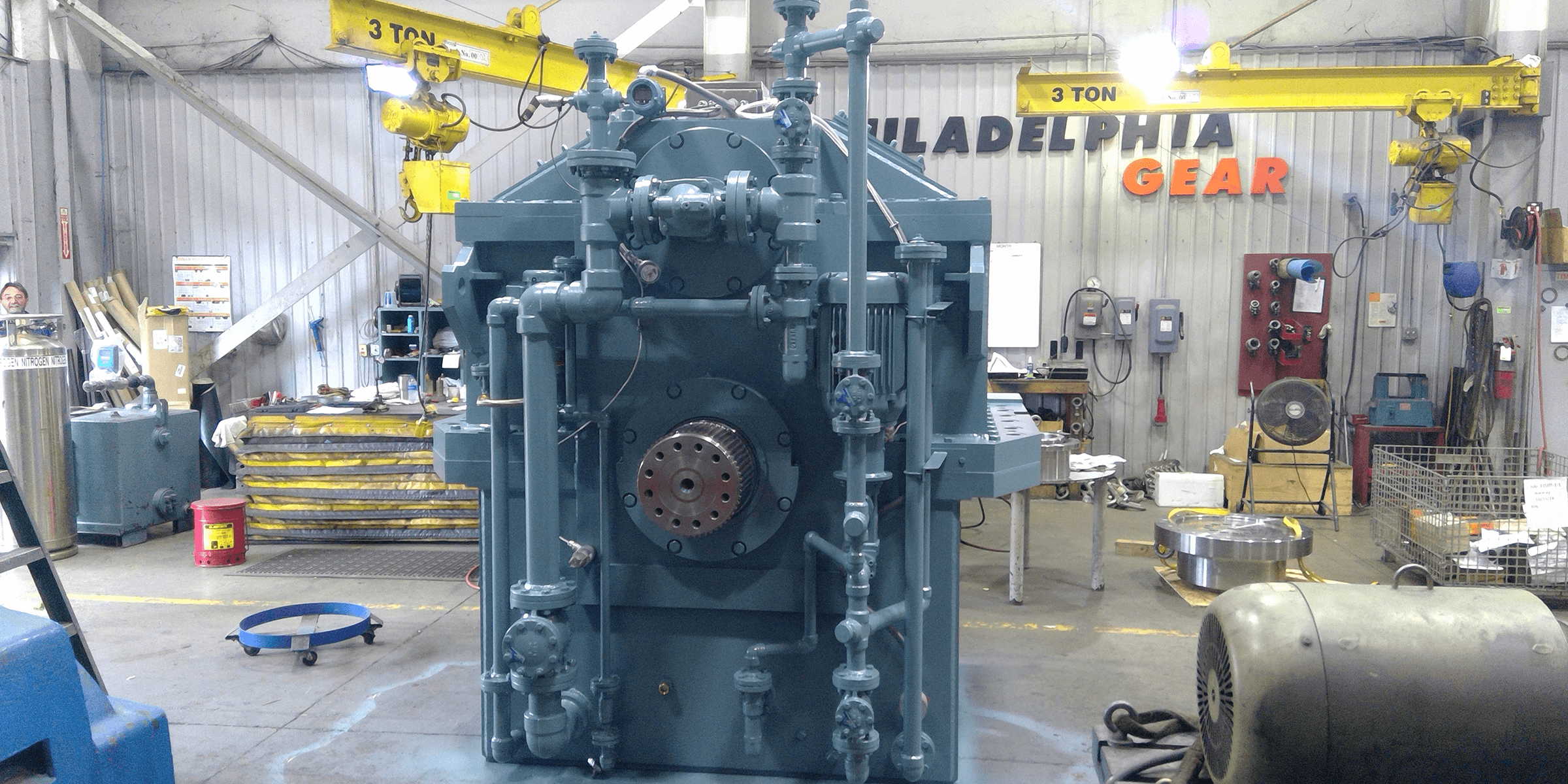
Q: What cost-effective alternatives are available for companies that don’t have the scale or revenue to justify the investment in spare gearboxes?
It’s not always necessary to replace an entire gearbox. There are maintenance measures that can help prevent unplanned downtime. Keeping spare components like gears, bearings and seals on hand can often solve many gearbox challenges, if the maintenance team has the capability to install them when needed.
Conducting regular inspections is one of the best ways to understand the health of your gearbox, whether you do it yourself or partner with a third-party expert like Philadelphia Gear. Vibration analysis and temperature sensors can also be installed so that a computer can analyze if there are any major changes in how the gearbox is operating.
We can also install sensors in key locations to help the operator monitor gearbox issues and fix problems before they lead to failure. Finally, taking samples of gearbox lubrication to determine what contaminants are present can provide clues about gearbox health and how to correct it. Often, this combination of spare components and predictive maintenance is sufficient for smaller companies, but they may still find it valuable to invest in spare gearboxes for crucial processes as their operations grow.
Maintenance teams with a solid understanding of gearbox design can set their facilities up for greater efficiency and productivity. Philadelphia Gear offers “Gear 101: An Introduction to Gearing Concepts and Elemental Gearbox Operation.” This four-hour program provides a concise yet comprehensive overview of gearboxes that can help maintenance professionals keep their plants running smoothly.