Case Study
Philadelphia Gear® Makes Maintenance Easier for Mine Operator
The Primary Challenge
Coal remains a crucial source for reliable electrical power generation as North America gradually transitions to more renewable energy technology. The majority of coal comes from surface mining operations, where gigantic equipment and highly-trained operators work together for maximum efficiency and productivity. Surface mines offer more than double the production of underground coal mines, with just one-third of the workforce.
One North Dakota surface mine produces 7.3 million short tons annually and operates adjacent to a 1100-megawatt power station generating electricity for two-thirds of rural Minnesota. Its biggest workhorses are two electric shovels measuring 45 ft. wide and 65 ft. tall — the height of a six-story building. Each shovel’s swing system is driven by two 1460-horsepower electric motors. The shovels operate 24/7/365 and feature buckets with the capacity to hold 64 cubic yards of coal at a time.
One of the shovels was due for routine maintenance, including a new swing gear drive. The swing gear drive works with a swing motor to rotate the shovel on the machine’s base. The existing unit showed signs of normal wear after more than 12 years of continuous operation. The maintenance team considered purchasing a replacement from the original equipment manufacturer, but was concerned about the OEM’s ability to offer satisfactory aftermarket service, delivery and support.
“Surface mines do important work but operate on very thin margins. They have no room for downtime,” says Jim Petruga, territory account specialist at Philadelphia Gear®, part of Timken Power Systems. “The maintenance team wanted to have confidence that a replacement swing gear drive would be ready for them to install by the time the shovel was offline for planned maintenance. They turned to us because of our engineering knowledge, manufacturing capabilities and track record serving other North American mines.”
The Solution
After identifying the manufacturer and technical specifications of the original swing gear drive, Petruga and his team consulted with Standard Machine®, another facility part of the Timken Power Systems network. Standard Machine is a leading aftermarket services and equipment provider to Canada’s mining industry. The company’s experts are highly-skilled at reverse engineering all types of gear drives and manufacture them in a state-of-the art, 175,000 sq. ft. facility in Saskatchewan, Canada.
Standard Machine uses a sophisticated database to store every gear drive design it’s ever made, including competing brands and original equipment designs by Timken Power Systems brands like Standard Machine, Philadelphia Gear, WesTech, Western and Hamilton Gear. The team quickly identified the competitor design needed by the customer, then retrieved the engineering drawings from the database. Standard Machine had previously reverse-engineered the design and produced it for another mine operator. The design featured two modular planetary gear cases and a single piece forged swing gear, which transmits torque for faster cycle times.
Due to the combined responsiveness of Philadelphia Gear and Standard Machine, the customer also requested support for maintenance training and automatic lubrication systems.
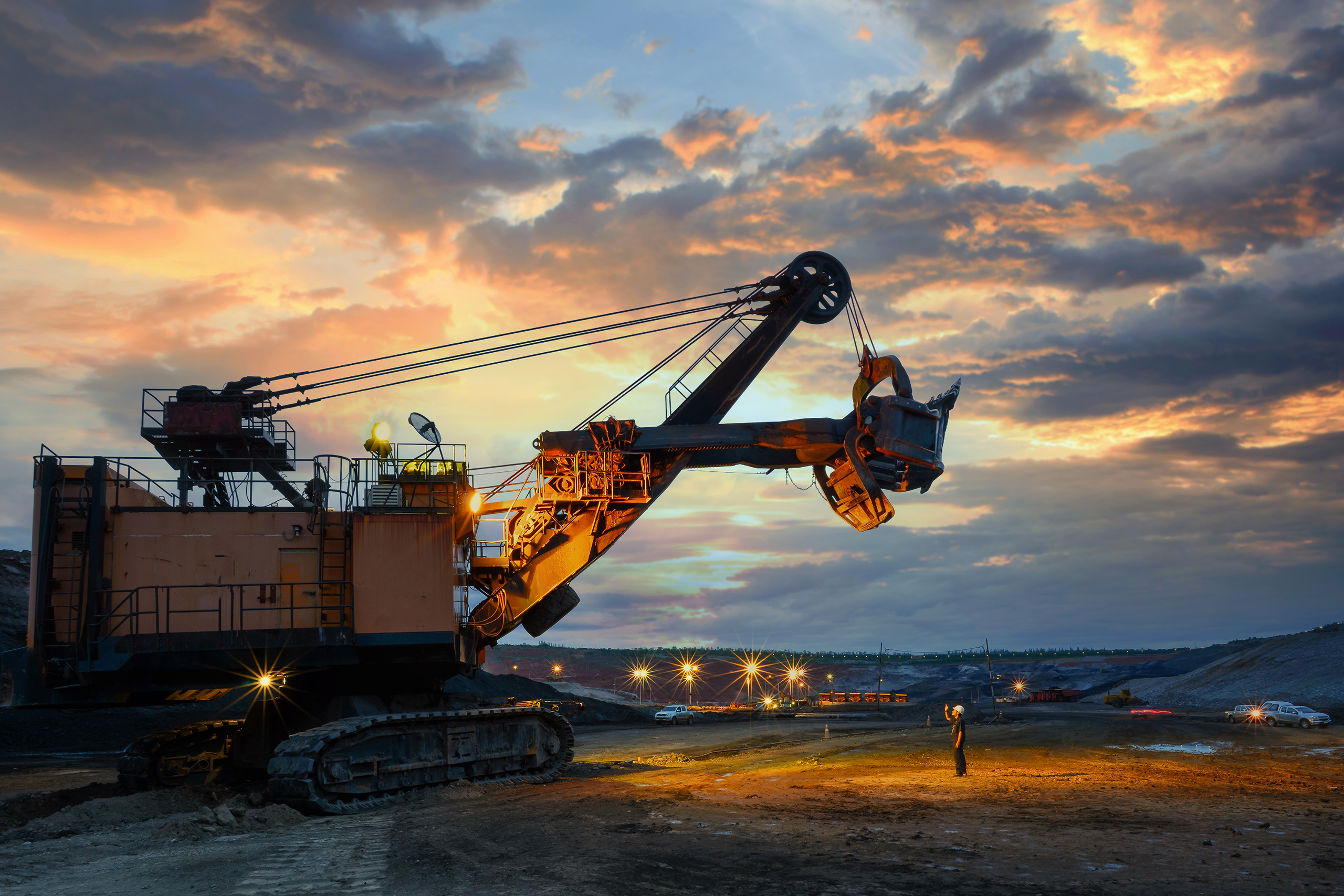
Key Results
Replacing the swing gear drive and other components helps maximize the mine’s equipment investment. A new electric shovel can cost millions of dollars.
The new swing gear drive is expected to operate as needed for decades with proper maintenance. Replacing the drive during regularly scheduled maintenance helped the mine avoid unexpected downtime and associated costs in the event that the original gear drive failed prior to replacement.
“Philadelphia Gear and Standard Machine leveraged our collective relationships and expertise to deliver an aftermarket solution where and when the customer needed it,” Petruga says. “Together we have 175 years of experience delivering industrial drivetrain solutions and 25 years of leadership in the mining industry. Few gear solutions providers have the breadth of capabilities like our combined companies.”
That goes for the capabilities of the companies’ individual team members, too. In particular, Petruga notes that John Stevenson, Philadelphia Gear’s business development manager for mining, and Jamie Connolly, planner and estimator at Standard Machine, played a crucial role in the success. “Their technical knowledge and fast turnaround with information,” he said, “helped keep the process moving forward to keep the customer on schedule.”
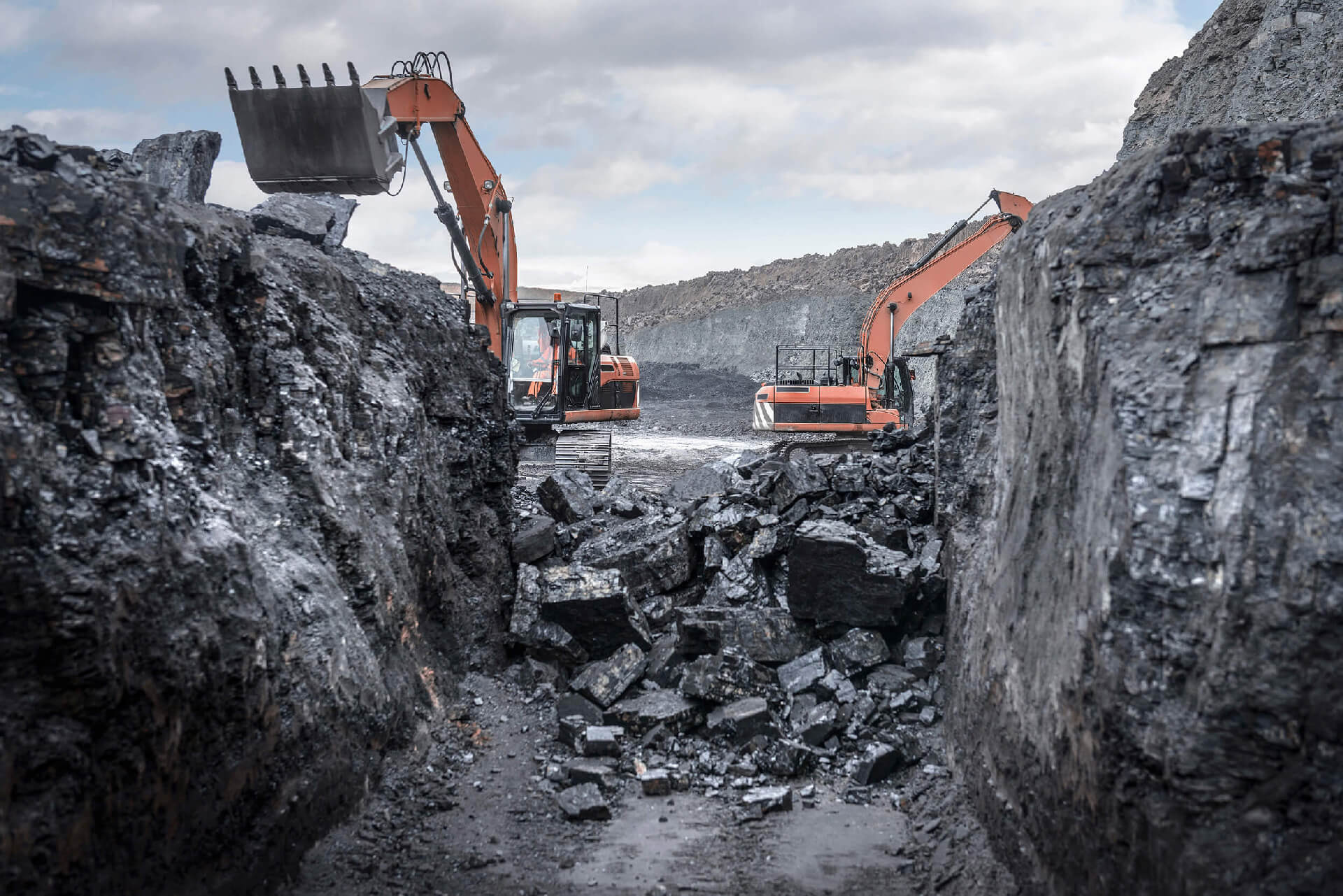