Case Study
Philadelphia Gear saves major chemical company hundreds of thousands of dollars with creative gear drive solution
In many instances, Philadelphia Gear’s technical expertise and repair skill can have a ripple effect that impacts people’s lives everywhere. We recently talked to an industry leader at Philadelphia Gear, with over three decades of experience as a machinist, about a recent successful re-engineering and gearbox repair job that excelled in the speed of delivery, the range of the repair services, and the time and cost savings for the client.
The Primary Gearbox Repair Challenge
A major chemical company located in the Midwest region contacted Philadelphia Gear to address a failure in their extruder gearboxes. These extruders are part of a critical process that produces pellets sold to automotive manufacturing plants that use them in spray guns to apply a protective coating on the inside of gas tanks of millions of cars on the road in the United States. This task requires demanding production schedules, often leading workers to push and stretch the electric motors and gearboxes that run the extruding process.
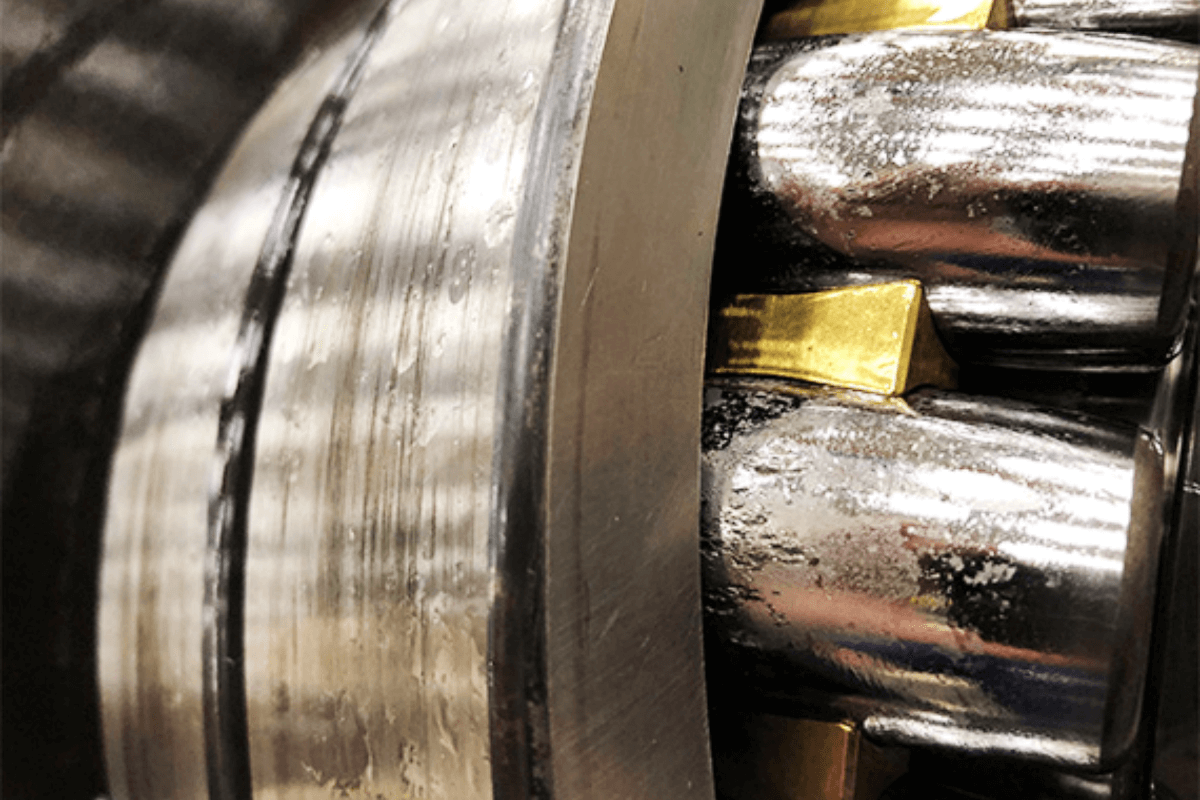
Two days before a routine inspection, the electric motor and gearbox were pulled out of service from one of the extruder systems after experiencing excessive vibration. Upon visual inspection, they saw that the first roto pinion shaft completely fractured off and was lodged in the electric motor’s rotor, so they sent the unit to Philadelphia Gear’s Midwest region regional service center for emergency repair. After disassembly and further inspection, they discovered the following additional damage:
- The 2nd roto shaft showed signs of wear, and excessive heat blackened the spline teeth and end journal
- Debris from bearings was found in the bottom of the gearbox
- The first intermediate bearing (on the low-speed end) was pitted on the rollers and inside the outer race
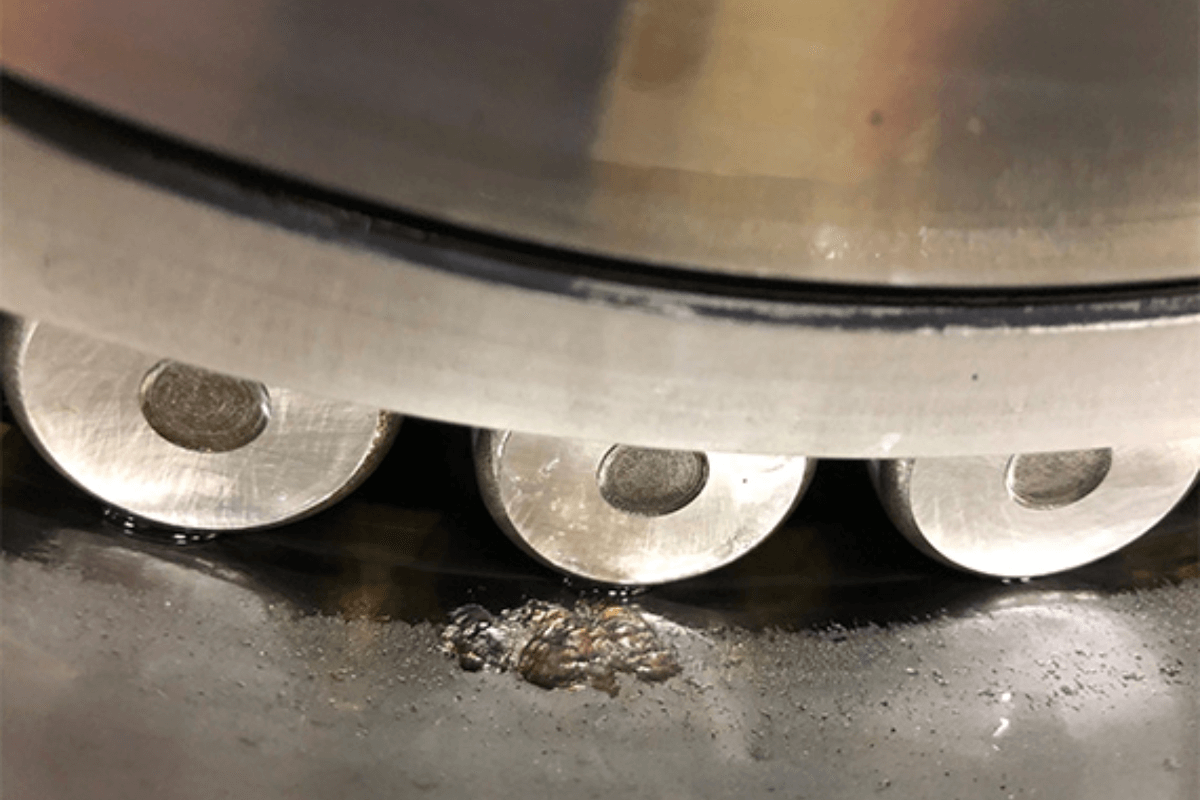
Gearbox Repair: Good Planning Saves the Customer Time and Money
Before the equipment failure, the customer had already developed a strong working relationship with the Philadelphia Gear Midwest team. In the course of servicing a few of their other extruder gearboxes, they found the same shaft problem across their whole line of non-Philadelphia Gear brand gearboxes they had in service. To correct the issue and save the customer the cost and time of replacing all the gearboxes, Philadelphia Gear engineers developed a set of re-engineered and upgraded low-speed shafts as spares for when they inevitably would fail during heavy operation. They designed them to be more durable and handle the increased torque loads that ultimately led the old sets to sheer off. This good planning paid off as it significantly cut down the lead time that would’ve been required to machine two new replacement shafts or replace the entire gearbox.
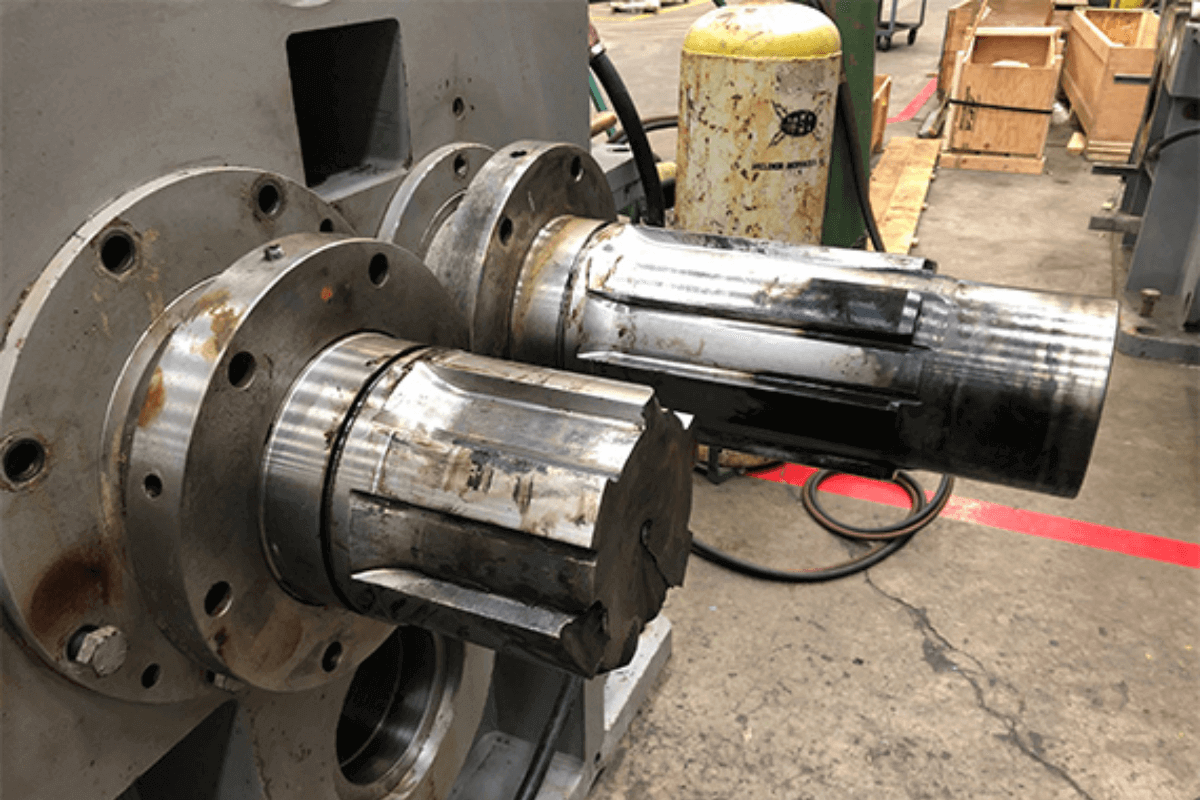
The Final Repair
The Philadelphia Gear team worked two intensive 10-hour shifts over the weekend to complete the gearbox repair. The project included all of the following:
- Installed customer spare 1st roto pinion shaft and 2nd roto shaft
- Replaced the high-speed, intermediate, thrust, and 1st and 2nd roto bearings
- Magnetic particle inspected (MPI) intermediate pinion shaft to confirm it could be reused (the pinion passed inspection)
- Installed new lip and labyrinth seals
- Performed MPI on and cleaned all existing gearing (passed inspection and was reused)
- Cleaned the interior and exterior housing
- Gearbox bores were deburred as needed and reused
- Caps and covers were cleaned and reused
- The unit was spin-tested for 90 minutes to confirm function and monitor and check bearing temperatures, vibration, and sound levels were within acceptable tolerances
- Repainted the housing
Results
“The estimated cost of downtime for the plant’s extruder production line is estimated to be up to $99,000 per day,” said Sean Duffy, territory account manager for Philadelphia Gear. “Understanding the problem and having the ready-made spares allowed us to move very quickly and perform a complete gearbox repair and reassembly in only two days, saving them hundreds of thousands of dollars and up to 16 weeks in downtime,” said Sean.
The customer was so pleased with the performance of Philadelphia Gear’s re-engineered components and the range of their gearbox repair services that they purchased four more spare shafts. “Our clients love our work and responsiveness, and they respect the level of care required to get it done right, even within tight deadlines. Usually, they prefer our work to the OEM,” finished Sean.
Philadelphia Gear, a division of Timken Power Systems, offers a wide range of gearbox repair services. From state-of-the-art predictive maintenance and diagnostics, the most complete set of equipment for testing and repairs, and engineering expertise for reverse engineering and component upgrades, Philadelphia Gear is a leader in both OEM gearbox repair and aftermarket gearbox repair for virtually any brand gearbox.