Keep your gearbox running efficiently — and free of ferrous metal contamination — with Philadelphia Gear’s CORE® system.
Short for Continuous Oil Rescue Equipment, this breakthrough technology removes contaminants as small as one micron, reducing damage and preserving your equipment and peace of mind.
REDUCE RISK. DRIVE EFFICIENCY
- Minimize the failure rate of your equipment
- Extend the life of your lubricant and equipment
- Reduce or eliminate your spare filter inventory
- Lower operating temperatures for your oil and equipment
- See no significant pressure drop as lubricant is pumped through
- Install filters upstream of the pump
- Easily clean and immediately return filters to service
- Protect your pump with minimal risk of cavitation
MICROSCOPIC PARTICLES CAUSE MASSIVE EQUIPMENT FAILURES
At this moment, ferrous metal wear particles are floating through your lubrication system, damaging your bearings, gears, and pinions. Over time, these particles cause reduced performance — and eventually, failure. While traditional barrier filtrations exist, their pressure drops make them incompatible with high-speed applications.
CORE® takes breakthrough filtering technology — originally developed for Formula One cars — and brings it to your application. Our proprietary design filters out particles as small as one micron (one millionth of a meter) to extend your gear drive’s regular operation time.
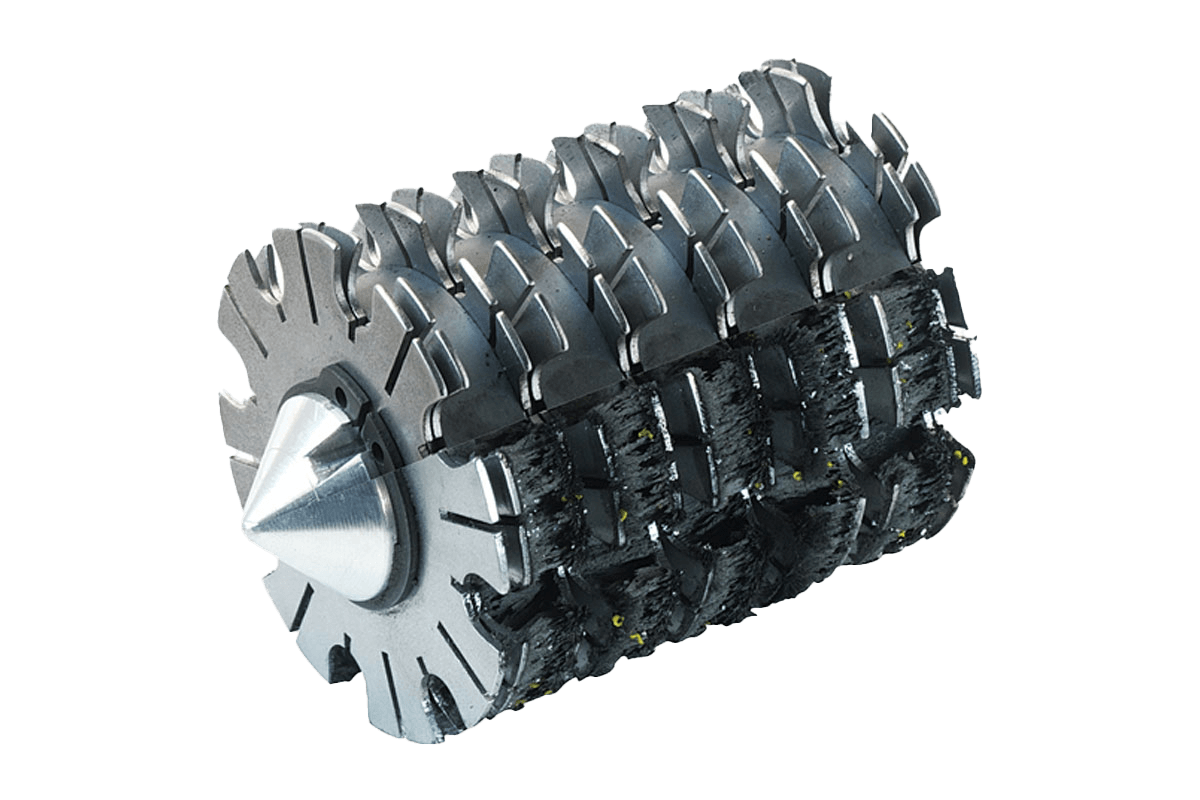
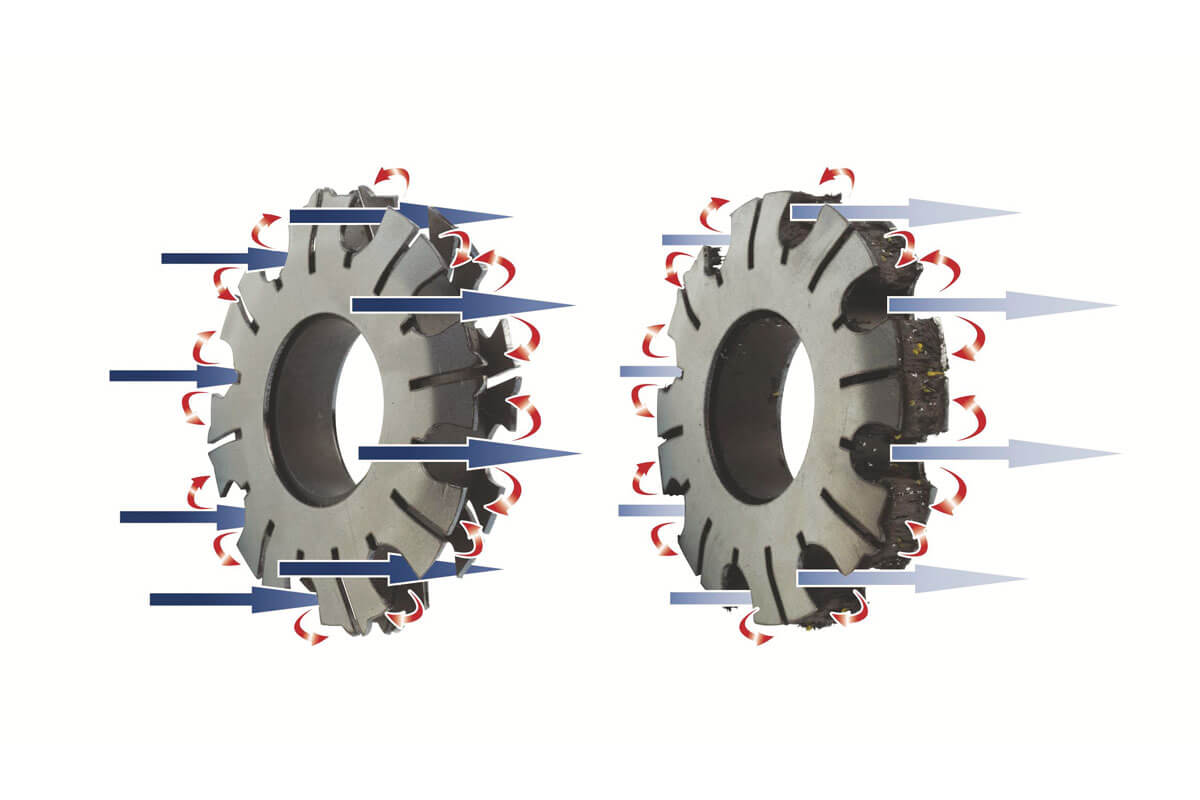
THE SCIENCE BEHIND CORE®
The CORE® system features a series of annular magnets shrouded by larger steel plates with flow channels. When oils of any viscosity flow through (represented by blue arrows), contaminants get drawn out by the magnetic fields (represented by red arrows) and into collection areas.
All this filtering occurs without a pressure drop, thanks to the CORE® system’s enlarged flow channel. CORE® compacts and isolates contaminants, keeping them out of the flow path and preventing wash-off — even when the filter is full. This also allows for fine filtration on the suction side of the pump, and more accessible condition monitoring of power transmission systems.
FREQUENTLY ASKED QUESTIONS ABOUT CORE®
The magnets inside CORE® have a half-life of 50 years. Built with high-grade aluminum housings, each CORE® unit is designed to outlive virtually any machine.
There are two versions of CORE®: The larger unit is designed for lube pipes with 1.25″ to 2.0″ diameter, and the smaller unit fits piping from 0.5″ to 1.25″ in diameter.
We generally recommend disassembling the unit, then using an 80 PSI air line, along with a blow off gun or nozzle, to clean the magnets and debris collection zones. This allows for efficient, effective cleaning, and preparation for reinstallation and reuse. Each CORE® unit also includes full cleaning instructions.
Disconnect the CORE® from the lube system and remove the flanged or threaded cover. We recommend doing this annually during the unit’s routine cleaning cycle, or more frequently for customers with highly contaminated lube systems.
The large unit holds up to two pounds of debris, and the small unit holds nearly one pound of debris.
CORE® can be configured in a duplex arrangement that doesn’t require shutting down for maintenance. If a duplex arrangement is not possible, the systems can also be piped in a “kidney loop” configuration so they can be valved off for cleaning.
The CORE® is designed to be compact. The large unit is 8” in diameter and 9.5” long at its widest and longest points, respectively. The smaller unit is 5” in diameter and 6.5” long.
The large system weighs approximately 10 lbs., and the smaller system weighs approximately 5 lbs.
There are several variables that impact the cost of the CORE® system, including how many units are purchased, whether they are in a single or duplex configuration, and which size CORE® is needed. One-off prices are $2,158 for the large unit and $1,617 for the small unit — a negligible amount compared to the cost of downtime, and accessible to even the tightest maintenance budgets.
Simply contact your nearest Philadelphia Gear Service Center, or call us at 800-766-5120.