Case Study
Philadelphia Gear® Marine Center of Excellence
Outfitted to Support the Needs of the U.S. Navy
“Swiss watches are known for operating efficiently and synchronously,” says Pete Yarger, general manager at Philadelphia Gear’s facility in Santa Fe Springs, Calif. “I tell people we basically produce 60-ton Swiss watches. Everything has to work perfectly.”
At the Santa Fe Springs facility, employees manufacture some of the largest and most complex products in the Philadelphia Gear® portfolio: main reduction gears (MRG) that help propel massive naval ships through all ocean conditions. Customers demand that these MRGs perform for at least 30 years. Most will operate for 45+ years.
Currently, the facility is manufacturing MRGs for the current class of CVN, DDG, LHA, LPD, and FFG vessels that will be in service into the 2080s. “We take a lot of pride in that,” Pete says. “Our focus is on quality and delivering best-in-class service through the duration of our products’ life span.”
The Market Leader in Naval Gear Systems
While Philadelphia Gear has provided gear systems and services to the U.S. Navy for nearly 100 years, 2008 was a pivotal year in strategic growth with the purchase of the intellectual property of General Electric’s marine gear product portfolio. The move was driven by a desire to acquire GE’s installed base and provide those customers with ongoing aftermarket service.
Philadelphia Gear has had operations in the area since 1996, but opened the current Santa Fe Springs facility in 2010 with a dual mission to build additional original equipment gear systems for the U.S. Navy and serve as the company’s Western Regional Service Center for industrial gear drives.
More than 90% of the facility’s customers build or operate naval ships. The Santa Fe Springs team uses the latest computer-controlled machine tools to manufacture ultra-precise gear drives and transmission solutions for those customers. The facility’s digitalized processes help the team achieve a level of precision and quality unmatched by many competitors.
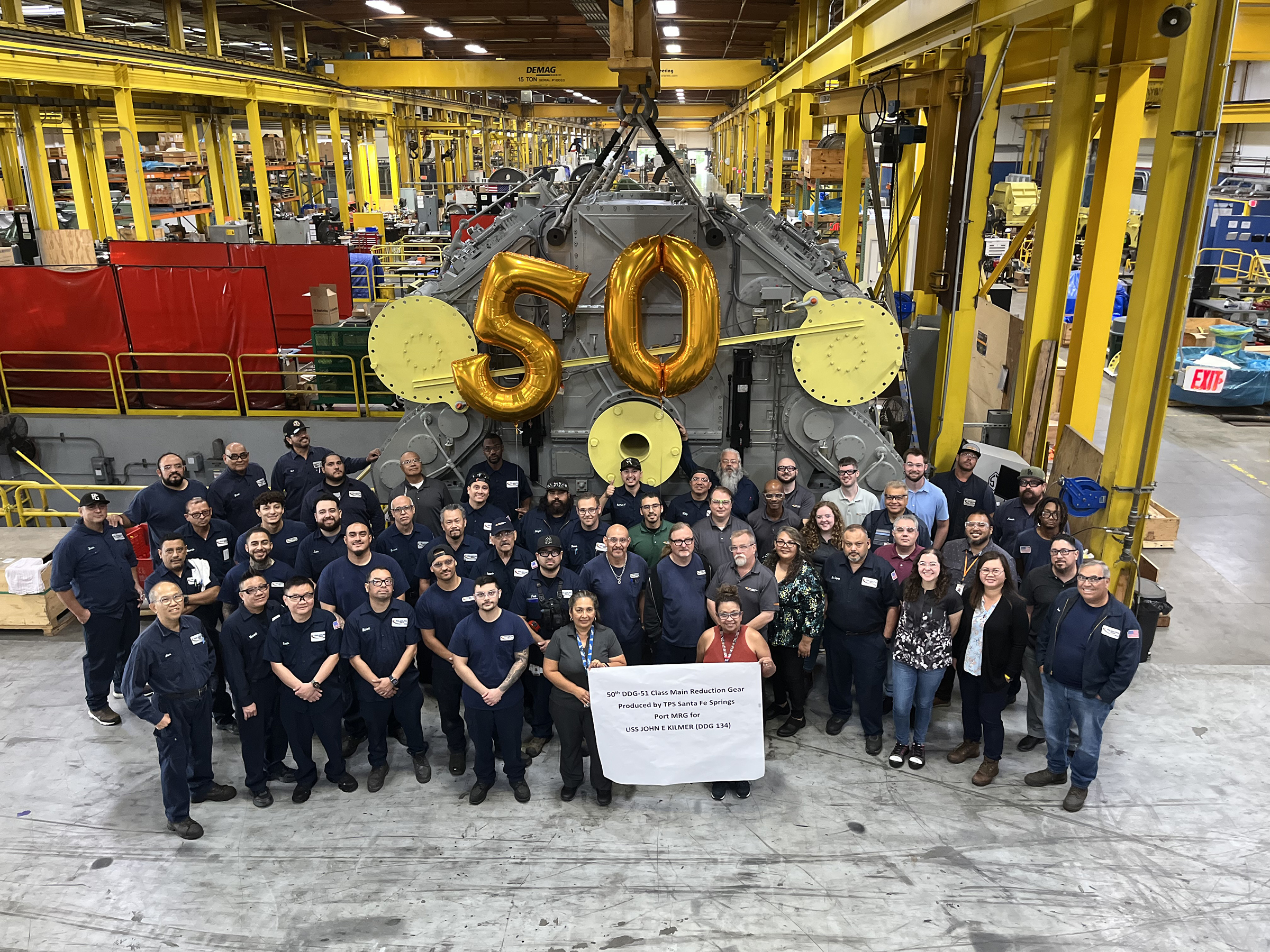
Connected to Meaningful Work
Pete notes the technology enables, but can’t replace, the team’s manufacturing expertise, knowledge and skills. It can take up to 18 months to build a single gear solution, and employees become very connected to their work.
“It’s not like they’re done making an MRG in a single shift,” Pete says. “Each individual personally works on a single product for up to three months. Machinists make the rotating elements. Assemblers put it together. Inspectors test it. If something isn’t right, they collaborate to fix it. We all take a lot of ownership because the process is so hands-on.”
Employees also are keenly aware of the real-world impact their work—partly due to the public nature of shipbuilding contracts, and also because Philadelphia Gear supports aftermarket service for naval ships all around the world. Nearly 20% of Santa Fe Springs employees are service veterans, who understand how important high-performing equipment is to peacekeeping missions.
“It’s tangible because we know exactly where our product goes,” Pete continues. “We’re reminded of the impact even years later when a ship is deployed on a mission, or we need to send one of our Onsite Technical Services (OTS)™ representatives abroad to troubleshoot an issue. Whether at port or at sea, we know our solutions help ships get to their destination and back home, reliably.”
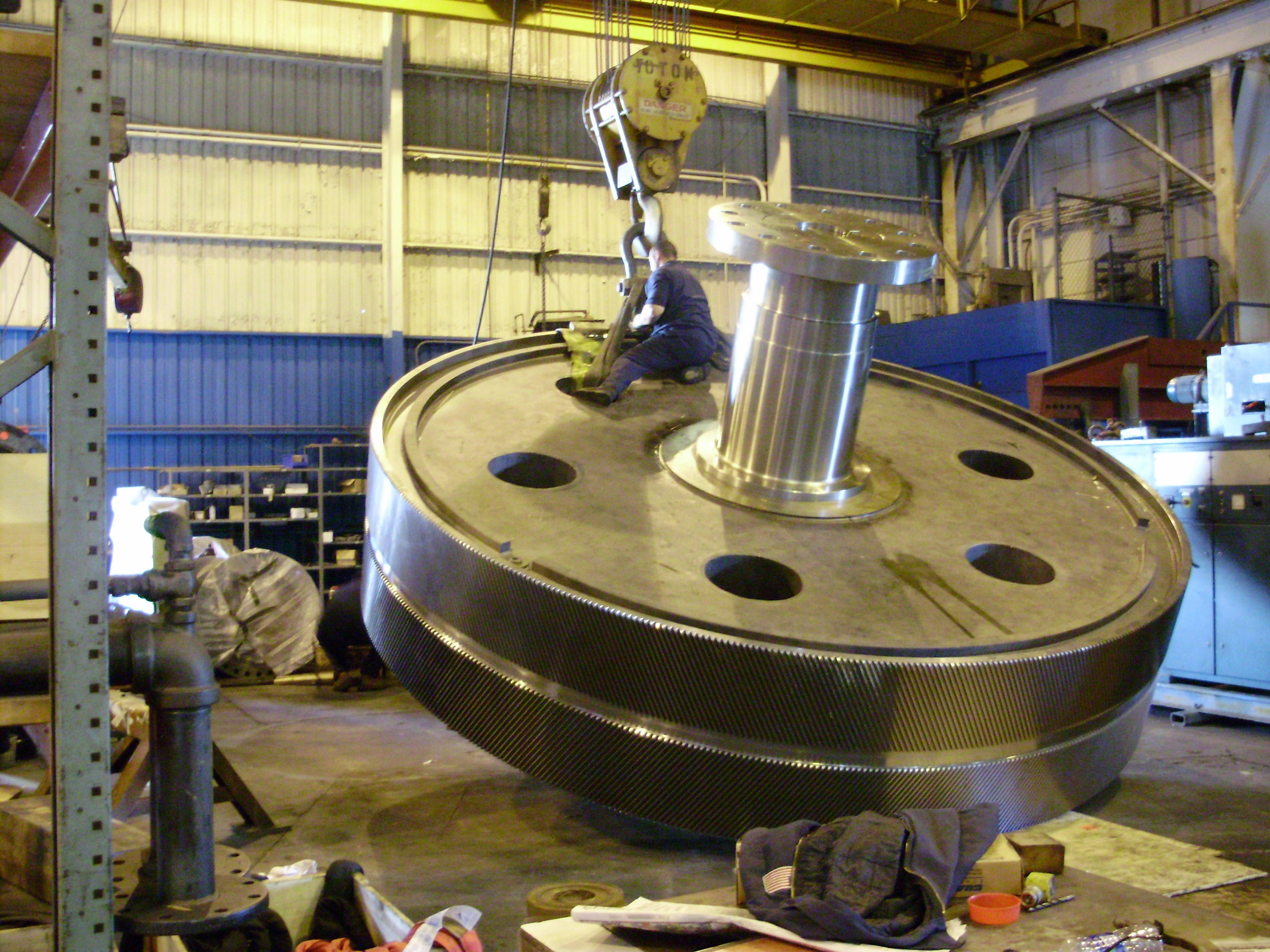