Case Study
Maximize Uptime: Planning Ahead to Avoid Equipment Failure
Keeping mission-critical equipment operational requires vigilance, regular maintenance and technical know-how from subject matter experts. Sometimes, engaging highly trained and qualified preventative maintenance and service experts can seem like an unnecessary expense, especially for smaller operations. But it can be a critical factor in avoiding costly and catastrophic equipment failure – especially in essential industries like energy.
Crucial machinery for critical resources
Coal-fired power stations provide approximately 40% of the world’s electricity and, in some regions, enable access to electricity to those who previously didn’t have it – increasing quality of life and reducing poverty. To keep the lights on worldwide, many facilities burn coal to make steam. The steam is forced through a series of pipes that amplify and release pressure to spin a series of turbines connected to generators that create electricity. Multiple types of equipment are used at these power stations, including pulverizers, which grind coal into a fine powder that can be flash ignited to create the steam required to run the power plant.
Without functioning pulverizers, coal-fired power stations can’t produce electricity. Since electricity can’t be stockpiled for an emergency, when a power plant does go down it must buy power from the grid so homeowners and businesses aren’t left in the dark.
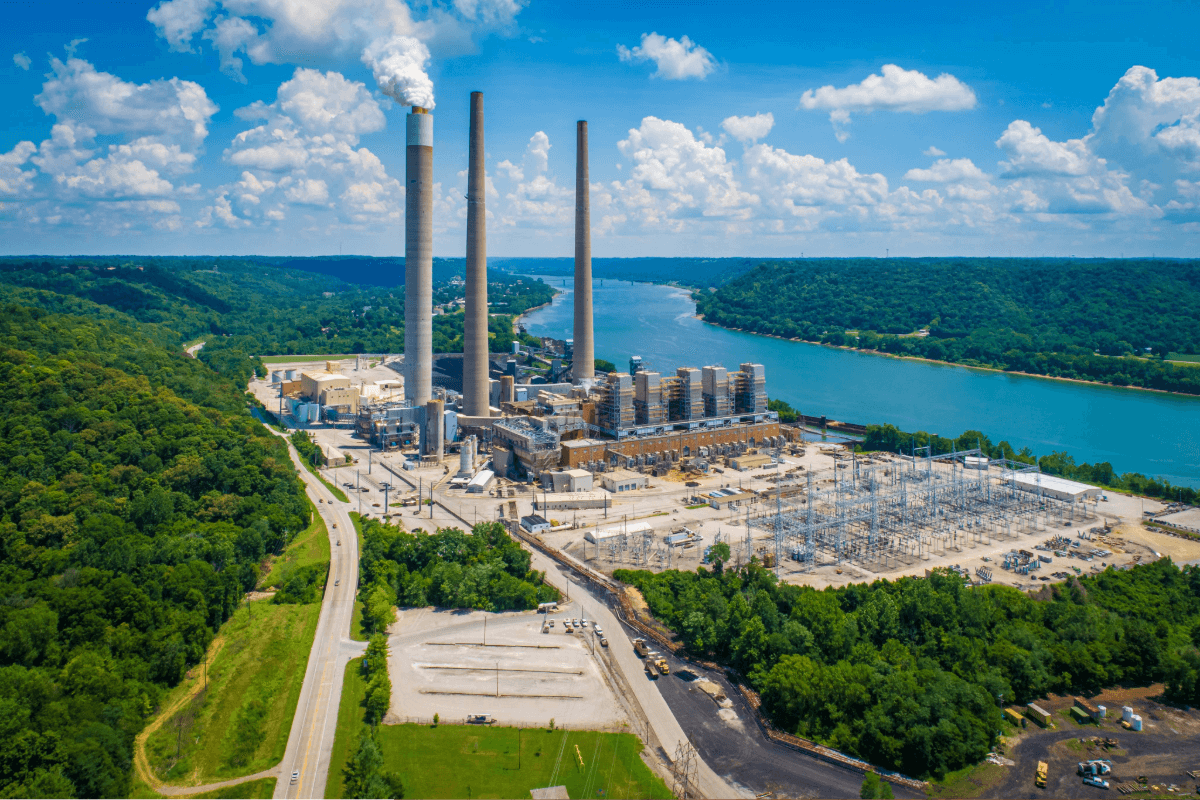
Investing in superior expertise matters
Properly maintaining and servicing pulverizer gearboxes is crucial for traditional energy production. Working with subject matter experts like the Philadelphia Gear® field service team can keep them running smoothly.
According to Brad Allen, Philadelphia Gear sales manager, field service plays a critical role in helping energy producers maximize uptime, reduce overall operating costs and, most importantly, provide uninterrupted service to communities. Choosing an experienced partner can save power stations precious time and money. Allen saw this firsthand when one energy customer experienced a high vibration reading on an input bearing in one of its facility’s six mission-crucial pulverizers.
“The vibration level wasn’t critical, but they wanted to have it repaired and back in service quickly,” Allen said. “We provided a quote for replacement bearings and field service. Pulverizers are not always easy to work on, so we recommended having the Philadelphia Gear field service team oversee the repair process since we have deep expertise in gearbox inspection and repair.”
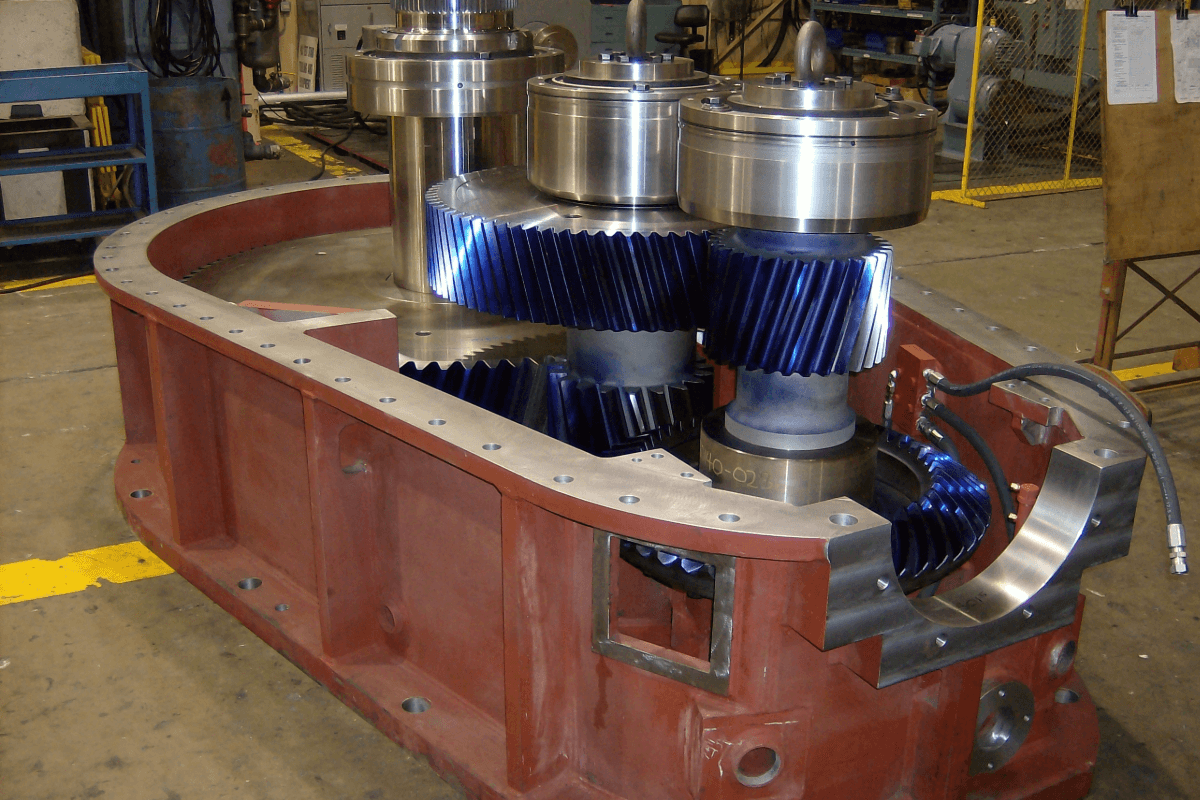
Instead, the customer opted to rely on a contracted third-party maintenance partner that was already providing onsite service. Three days later, Allen received a call. Teeth had been broken off the gearbox’s bevel gear during the removal of the pulverizer’s input cylinder – resulting in the need for a new gear set. At the time, lead times for a new gear set were lengthy due to supply chain challenges and market conditions.
With the power station’s maintenance team in a bind, they reached out to Philadelphia Gear for help. The original repair scope grew from involving a quick bearing replacement to now manufacturing and installing an entirely new gear set. While Philadelphia Gear expedited the order, the pulverizer was still forced offline for a much longer period than originally expected. The failure put the plant at a higher risk of not meeting production demand if its second pulverizer failed.
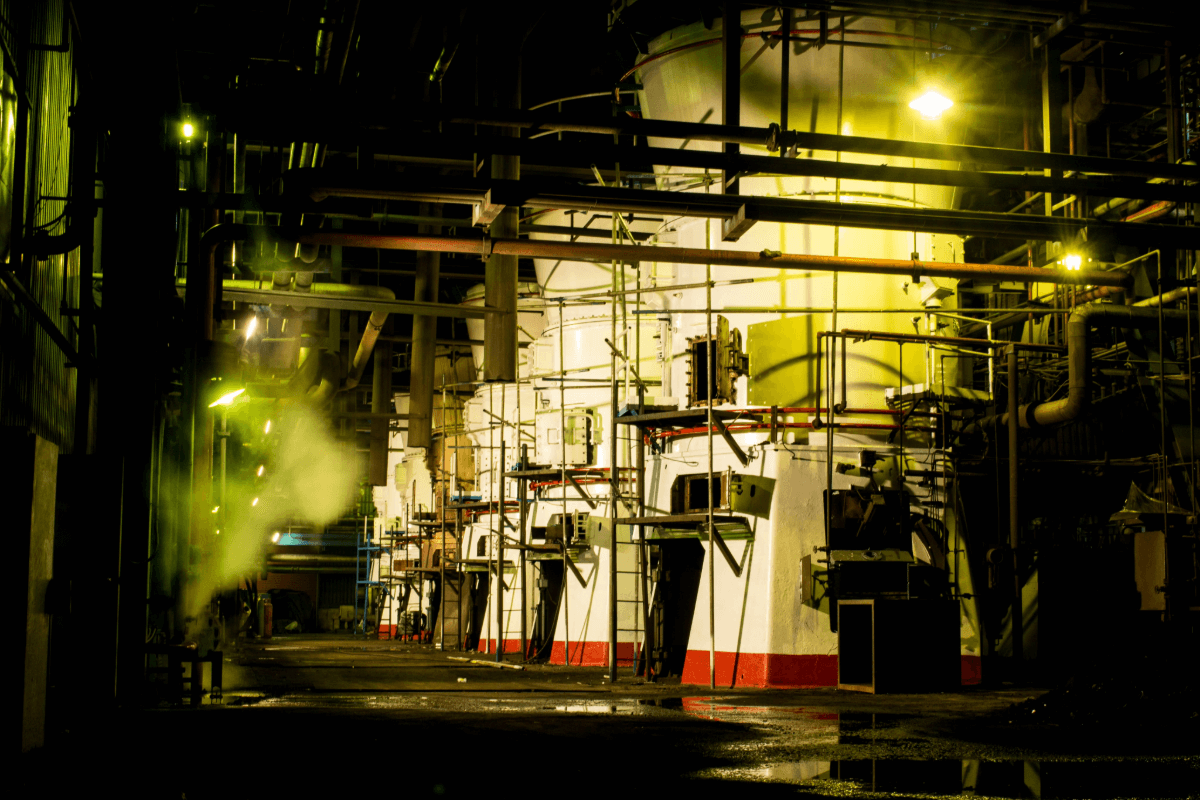
Trusted partners help companies save money in the long-term
Ultimately, what would have been up to a $16,500 expense to engage Philadelphia Gear’s Onsite Technical Services in overseeing the replacement of $40,000 in bearings turned into nearly a $1 million expense to replace all bearings and gears on a rush delivery timeline. The customer also lost valuable production capacity while the pulverizer was out of service.
In addition to teaming up with a highly experienced technical services team, keeping a spare gearbox on hand can also help companies improve uptime and operate cost-effectively. Learn more in this Q&A with Ted Pratt, account specialist.
“A small upfront investment could have helped avoid this entire situation,” Allen said. “Working with an experienced field service team can help energy customers, and anyone operating heavy industrial equipment, avoid catastrophic failures and downtime.”