Case Study
Quick turnaround time helps plant save thousands in energy costs
A large plant that produces over 850,000 tons of salt per year in the United Kingdom, contacted the Philadelphia Gear European sales office when their accessory gearbox failed. Due to the extensive power requirements to meet production needs, the facility houses an on-site power plant driven by a large gas turbine that’s connected to a non-Philadelphia Gear brand accessory gearbox. The drive transmits power between a starter (diesel engine) and a turbine, and contains a large integral oil pump that provides lubrication for the entire system. With the drive out of service, the turbine was at a standstill forcing the plant to pull power from the local energy grid to keep production running, a much more costly alternative
To evaluate the problem, a sales representative from the European office was deployed. During visual inspection, discoloration on the #1 and #2 shaft assemblies was discovered, indicating severe damage and the need for a replacement set. He contacted the Southeast Regional Service Center, in Birmingham, Alabama, for an estimated lead time for the repair. They were able to offer a three-week turnaround time, approximately seven to ten weeks shorter than the industry standard. With the plant paying high power consumption penalties and confident that Philadelphia Gear could handle the project, they made the decision to ship the gearbox overseas for an emergency repair at the Birmingham facility.
Pending the arrival of the drive, team members at the Birmingham facility began machining new assemblies and procuring parts. Importing the gearbox to the US facility was a challenge, but the Customer Service team at Birmingham was able to acquire a temporary import bond, to expedite the shipment.
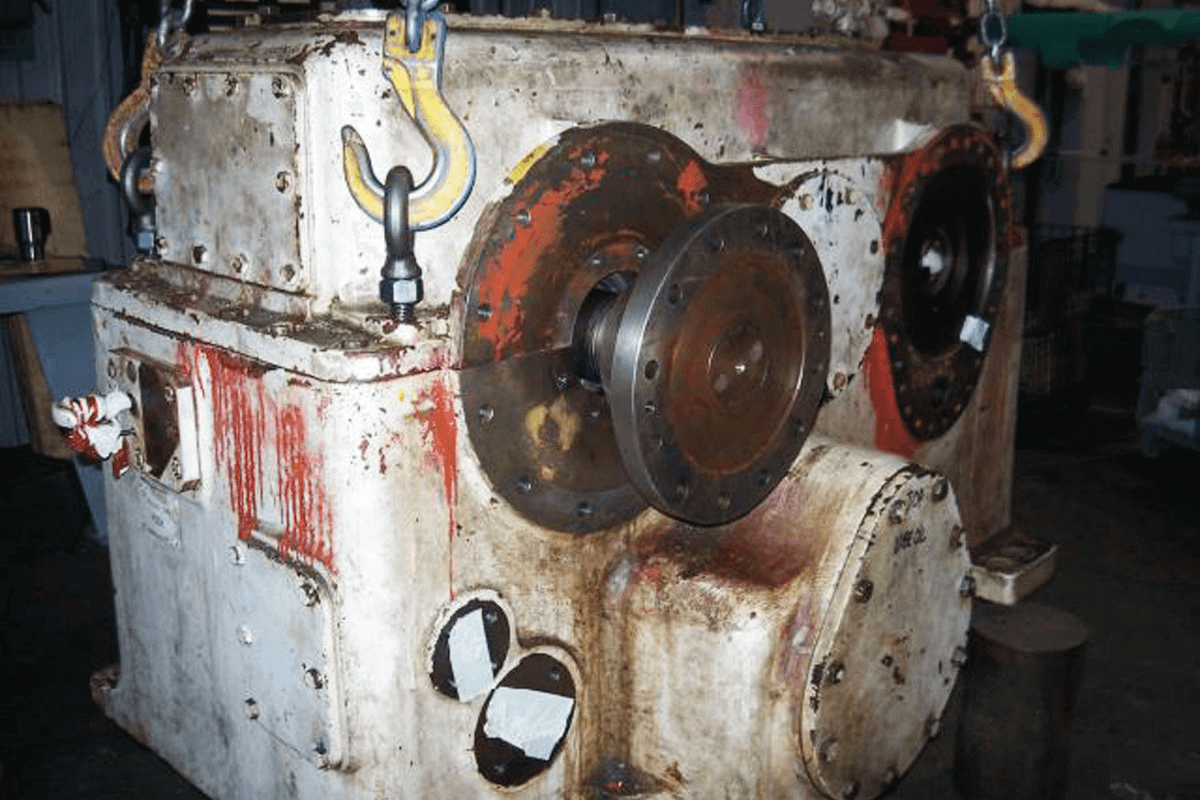
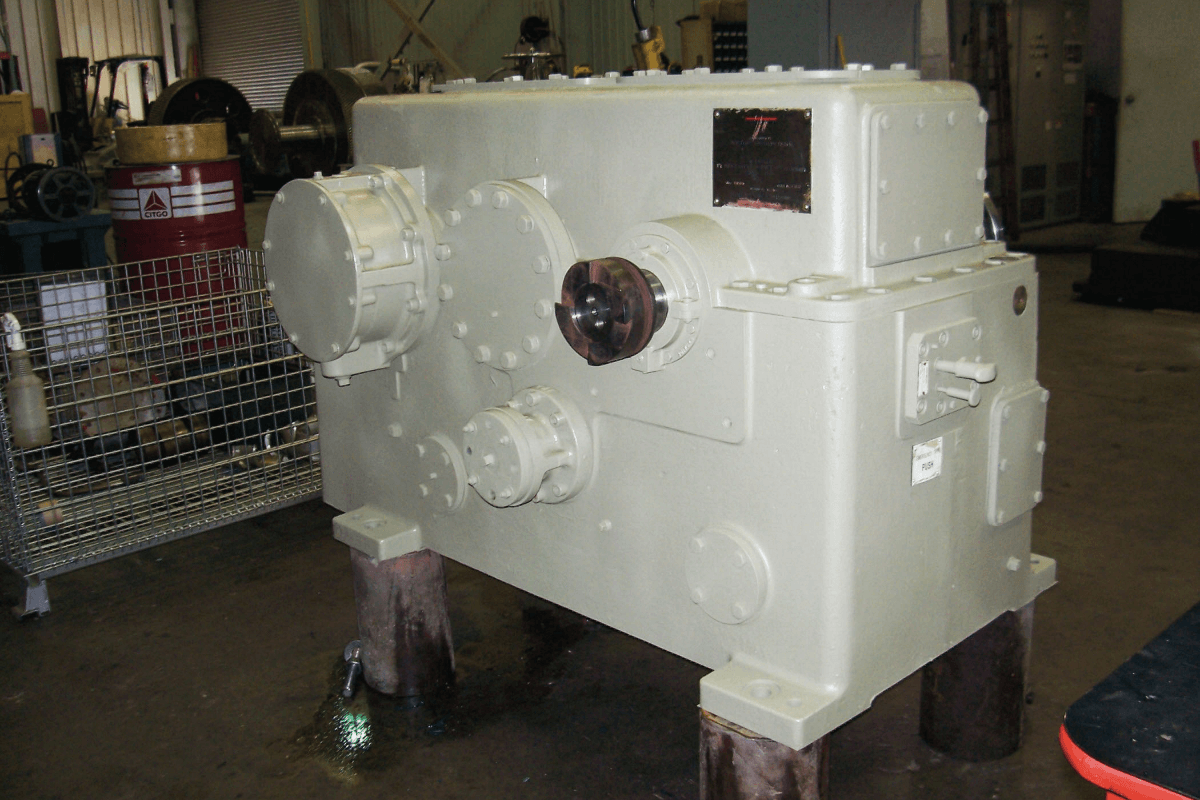